The Benefit of Speed, Scale & Quality | Explore Samsung Biologics' CMO Strengths
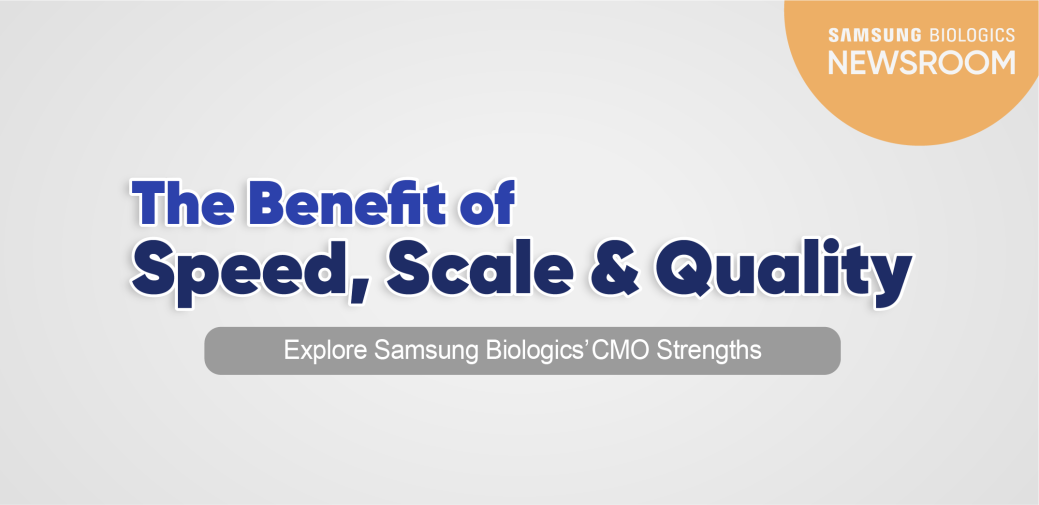
The Benefit of Speed, Scale & Quality
Explore Samsung Biologics'CMO Strengths
As the global biopharmaceutical market continues to expand rapidly with a greater market demand for biopharmaceutical products due to an aging population, a rising number of diseases and the resulting treatments, now more than ever, companies are choosing to strategically outsource their manufacturing activities to ‘contract manufacturing organization (CMO)’ partners like Samsung Biologics to get their products to market with speed, quality and in the most cost effective way possible.
In this article, we will explore the services a CMO can provide and the benefits the right partner can bring to projects. We will also showcase Samsung Biologics’ unique strengths and capabilities as one of the world leading CMOs with the world’s largest manufacturing capacity on one single site.
What does a CMO Offer its Clients and What are the Benefits?
To ensure the successful delivery of biomedicines a biopharmaceutical company must be fully equipped with the right capabilities and available capacity to manufacture products at any scale and, be able to accommodate the evolving needs in the market. In order to deliver proven-quality biomedicines to patients, a CMO must be able to strictly control quality across its facilities and its manufacturing processes according to GMP (Good Manufacturing Practice) standards.
(*Please refer to the article “What are Biomedicines” for more information.)
With these complex requirements, bringing products to the market safely and on time can be a challenging process. This combined with the surging demand for biopharmaceuticals means that companies are looking for outsourcing partners who can manufacture their products with speed, flexibility, and up-to-date technology. Successful outsourcing can allow them to focus their internal efforts on research and discovery of new treatments, while ensuring development and commercialization of existing products is done reliably. Outsourcing also allows companies to save heavily on investment costs to expand their own development and manufacturing facilities.
Biopharmaceuticals: The Journey for Successful Manufacturing
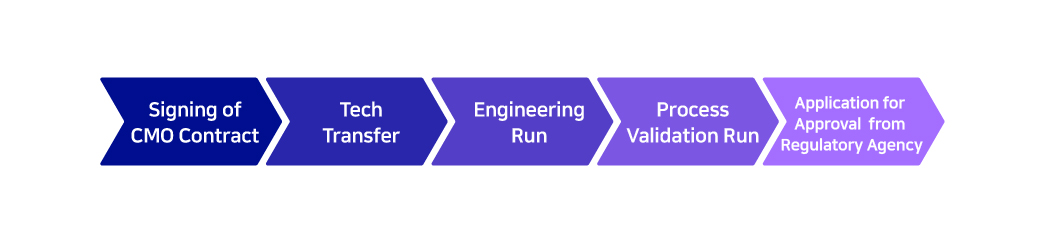
- Single of CMO Contract
- Tech Transfer
- Engineering Run
- Process Validation Run
- Application for Approval from Regulatory Agency
Upon signing a CMO contract with a client, a complex journey begins to ensure successful manufacturing of biopharmaceuticals. A process called ‘Tech Transfer’ is required to manufacture a molecule that is developed by the client. This involves the transfer of technologies including the manufacturing processes, analysis methods, and testing methods into the CMO partner’s facility. Afterwards, processes called the ‘Engineering Run’ and ‘Process Validation Run’ are conducted to optimize the variables during the manufacturing process, the pilot-scale manufacturing is completed and product’s stability is verified throughout every stage of the process.
Only after completing the in-house manufacturing preparation processes can a CMO apply for manufacturing approval of production goods and processes for certification to international regulatory agencies, such as the FDA and the EMA. Once the processes have been approved, large-scale manufacturing can begin.
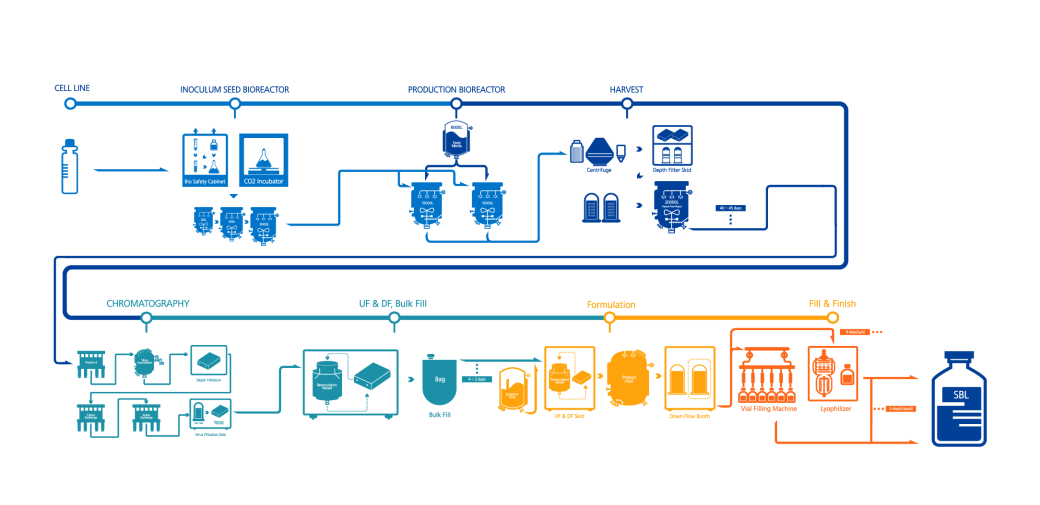
- CELL LINE
- INOCULUM SEED BIOREACTOR
- PRODUCTION BIOREACTOR
- HARVEST
- CHROMATOGRAPHY
- UF & DF, Bulk Fill
- Formulation
- Fill & Finish
Drug products that can be administered to patients are determined only after manufacturing high-quality target proteins in the ‘Cell Culture’ process, extracting only the target antibodies to produce the drug substance (DS) in the ‘Purification’ process. The ‘Aseptic Fill/finish’ process is completed once all of these processes have been conducted. All manufacturing processes strictly abide by the global GMP standards.
Samsung Biologics’ Unique Strengths for Contract Manufacturing Services
Samsung Biologics currently has the world’s largest biomanufacturing facility in terms of capacity, with the ability to produce up to 364,000 liters at a single site.
We have four plants at our site in South Korea. Plant 1 holds an industry standard of 30,000L, and Plants 2 and 3 each offer 154,000L and 180,000L respectively. Upon Plant 4’s completion in 2023, Samsung Biologics will hold a total biomanufacturing capacity of 620,000 liters while offering multi-scale manufacturing services from 1K, 2K, 5K, 10K, and 15K to flexibly respond to all of the clients’ needs at any scale.

- Plant 1 Cell culture capacity 5K x 6 = 30,000L
- Plant 1 Capability Liquid & Lyo vials
- Plant 1 CGMP ready Jun. 2013
- Plant 1 Laboratories QC Laboratory
- Plant 2 Cell culture capacity (1.5K x 10) + (1K x 2 SUS) + (1K x 2 SS) = 154,000L
- Plant 2 Capability Liquid & Lyo vials
- Plant 2 CGMP ready Fed. 2013
- Plant 2 Laboratories PD Laboratories
- Plant 3 Cell culture capacity 15K x 12 = 180,000L
- Plant 3 Capabillity Fed-batch with N-1 perfusion capability
- Plant 3 CGMP ready Oct. 2018
- Plant 3 Laboratories QC Laboratory, PD Laboratories
- Plant 4 Cell culture capacity (15K x 12) + (10K + 6) + (2K + 8) = 256,000L
- Plant 4 Capabillity Multi-scale, digitalizations, automation, eco-friendly
- Plant 4 CGMP ready Expercted by. 2023
- Plant 4 Laboratories QC Laboratory, PD Laboratories
Samsung Biologics offers ‘one-stop services’ that not only includes contract manufacturing but development and testing services too, allowing us to support the full product lifecycle for our customers. We are fully equipped to accommodate projects of all shapes and sizes while reducing manufacturing time and overall cost.
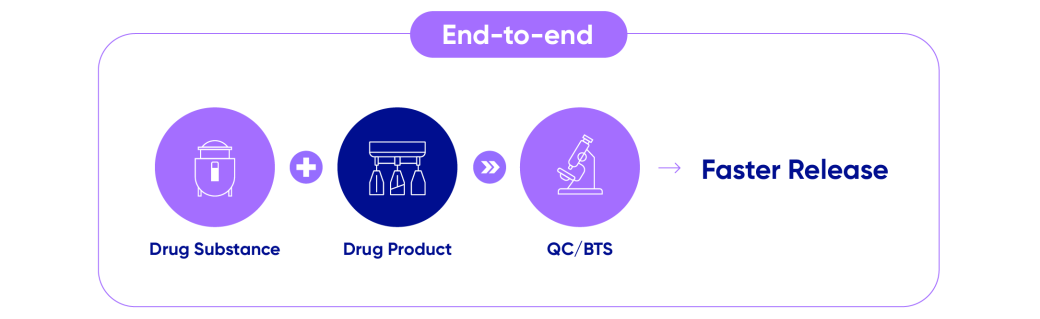
- Drug Substance
- Drug Product
- QC/BTS
- Faster Release
By offering fully-integrated services to our clients, we can ultimately reduce the potential for time delays as well as the risk of information leaks whilst ensuring consistent quality. For example, Samsung Biologics’ drug product (DP) services recently reduced time for tech transfer to 2-3 months - half the industry average of 6 months - for verification of batch production to expedite the process and deliver urgent biopharmaceuticals to treat COVID-19.
As a means to further increase client satisfaction, we also have state-of-the-art manufacturing capabilities, such as N-1 Perfusion* and EQUIS**, to improve cell density, reduce production time, and improve productivity, as well as advanced digital technologies such as our ‘Live Virtual Tour (LVT)’ system which was preemptively introduced in early 2020 in light of COVID-19. The LVT gives our clients and regulatory agencies remote access to our online system anywhere in the world and the ability to conduct virtual due diligence safely and effectively.
* N-1 Perfusion: Advanced cell culture technology that improves productivity by reducing production time.
** EQUIS (Enterprise Quality Unified Information System): A system that can record and manage documents and quality records in real time.
The Final Hurdle: Successful Aseptic Fill & Finish
Samsung Biologics has shown a rapid growth rate for its aseptic fill/finish business area since it started the business and has become well-known for its quality and speed. Aseptic fill/finish is the final stage of the manufacturing process before patient administration, and as such requires adherence with complex standards for facility operation and management, as well as manufacturing processes to ensure thorough aseptic treatment while maintaining the strictest care for quality.
In addition, the stability for product quality is crucial for this particular stage as it is the only process where the product is externally exposed prior to administration. Samsung Biologics has obtained a total of 16 approvals for its aseptic fill/finish from major agencies including the U.S. Food and Drug Administration (FDA), the European Medicines Agency (EMA), and the Japanese Organization for Medical Devices (PMDA) giving us an impressive track record when it comes to successfully completing aseptic fill/finish projects.
We also have plans to expand our facilities for the manufacturing of both mRNA vaccine drug substance and drug product allowing us to commence manufacturing for vaccines in 2022 and become Asia’s central hub for vaccine supply.
Fully Integrated CDMO Partner: A Track Record to Inspire Trust
To date, we have multiple manufacturing contracts with some of the world’s leading biotech companies, including the manufacturing of COVID-19 treatments and vaccines. Samsung Biologics has obtained a total of 92 global approvals from international certification agencies as of May 2021 and is still growing, affirming its leading capabilities and bolstering its position as a recognized and trusted CDMO partner.
Since its establishment in 2011, Samsung Biologics has continued to evolve to ensure we continue to manufacture high-quality biopharmaceuticals for our customers. We do this through our dedication to continuous innovation and by ensuring the strictest care for quality.
Samsung Biologics was awarded the ‘CMO Leadership Awards,’ an industry-recognized award, in 2013 for successfully achieving client satisfaction and quality competitiveness, while quickly responding to changes in the market environment and providing life-saving solutions to patients worldwide.
Our team continues to offer a fully integrated, end-to-end manufacturing services to its clients to enhance both the global and local supply network of biopharmaceuticals and to save lives of many people in urgent need worldwide.
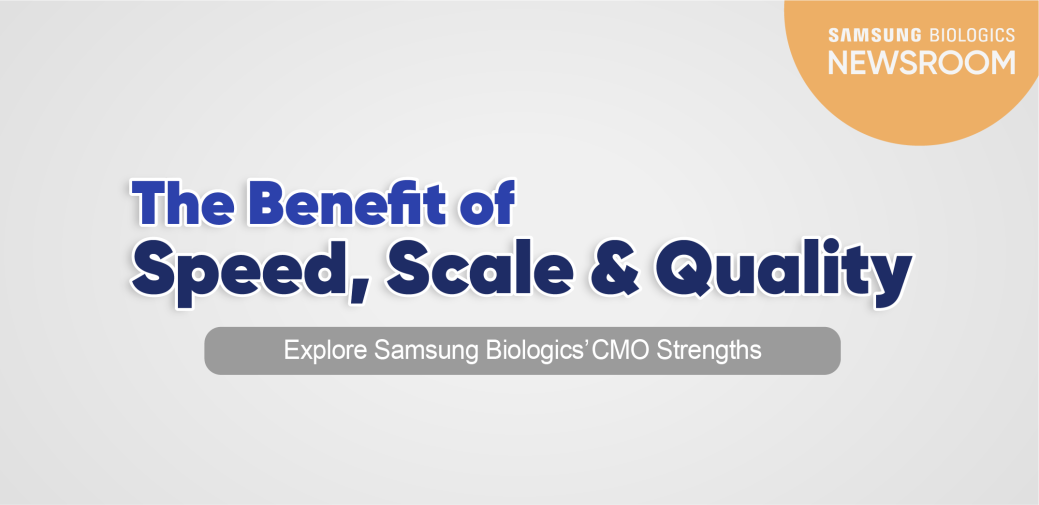
The Benefit of Speed, Scale & Quality
Explore Samsung Biologics'CMO Strengths
As the global biopharmaceutical market continues to expand rapidly with a greater market demand for biopharmaceutical products due to an aging population, a rising number of diseases and the resulting treatments, now more than ever, companies are choosing to strategically outsource their manufacturing activities to ‘contract manufacturing organization (CMO)’ partners like Samsung Biologics to get their products to market with speed, quality and in the most cost effective way possible.
In this article, we will explore the services a CMO can provide and the benefits the right partner can bring to projects. We will also showcase Samsung Biologics’ unique strengths and capabilities as one of the world leading CMOs with the world’s largest manufacturing capacity on one single site.
What does a CMO Offer its Clients and What are the Benefits?
To ensure the successful delivery of biomedicines a biopharmaceutical company must be fully equipped with the right capabilities and available capacity to manufacture products at any scale and, be able to accommodate the evolving needs in the market. In order to deliver proven-quality biomedicines to patients, a CMO must be able to strictly control quality across its facilities and its manufacturing processes according to GMP (Good Manufacturing Practice) standards.
(*Please refer to the article “What are Biomedicines” for more information.)
With these complex requirements, bringing products to the market safely and on time can be a challenging process. This combined with the surging demand for biopharmaceuticals means that companies are looking for outsourcing partners who can manufacture their products with speed, flexibility, and up-to-date technology. Successful outsourcing can allow them to focus their internal efforts on research and discovery of new treatments, while ensuring development and commercialization of existing products is done reliably. Outsourcing also allows companies to save heavily on investment costs to expand their own development and manufacturing facilities.
Biopharmaceuticals: The Journey for Successful Manufacturing
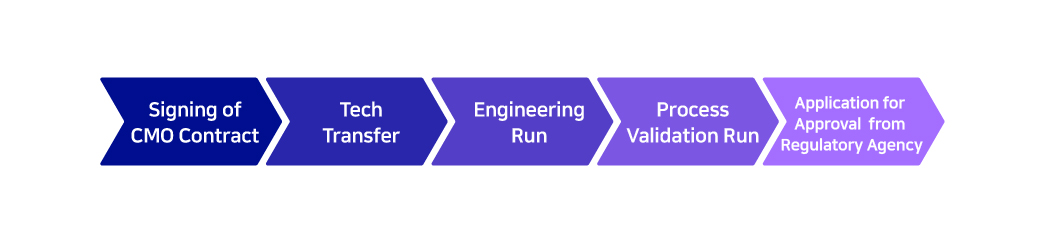
- Single of CMO Contract
- Tech Transfer
- Engineering Run
- Process Validation Run
- Application for Approval from Regulatory Agency
Upon signing a CMO contract with a client, a complex journey begins to ensure successful manufacturing of biopharmaceuticals. A process called ‘Tech Transfer’ is required to manufacture a molecule that is developed by the client. This involves the transfer of technologies including the manufacturing processes, analysis methods, and testing methods into the CMO partner’s facility. Afterwards, processes called the ‘Engineering Run’ and ‘Process Validation Run’ are conducted to optimize the variables during the manufacturing process, the pilot-scale manufacturing is completed and product’s stability is verified throughout every stage of the process.
Only after completing the in-house manufacturing preparation processes can a CMO apply for manufacturing approval of production goods and processes for certification to international regulatory agencies, such as the FDA and the EMA. Once the processes have been approved, large-scale manufacturing can begin.
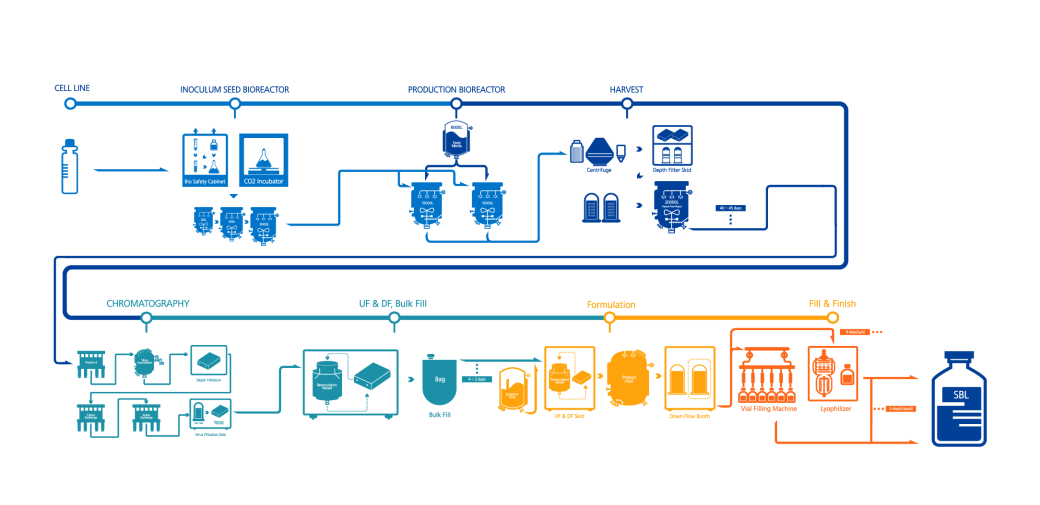
- CELL LINE
- INOCULUM SEED BIOREACTOR
- PRODUCTION BIOREACTOR
- HARVEST
- CHROMATOGRAPHY
- UF & DF, Bulk Fill
- Formulation
- Fill & Finish
Drug products that can be administered to patients are determined only after manufacturing high-quality target proteins in the ‘Cell Culture’ process, extracting only the target antibodies to produce the drug substance (DS) in the ‘Purification’ process. The ‘Aseptic Fill/finish’ process is completed once all of these processes have been conducted. All manufacturing processes strictly abide by the global GMP standards.
Samsung Biologics’ Unique Strengths for Contract Manufacturing Services
Samsung Biologics currently has the world’s largest biomanufacturing facility in terms of capacity, with the ability to produce up to 364,000 liters at a single site.
We have four plants at our site in South Korea. Plant 1 holds an industry standard of 30,000L, and Plants 2 and 3 each offer 154,000L and 180,000L respectively. Upon Plant 4’s completion in 2023, Samsung Biologics will hold a total biomanufacturing capacity of 620,000 liters while offering multi-scale manufacturing services from 1K, 2K, 5K, 10K, and 15K to flexibly respond to all of the clients’ needs at any scale.

- Plant 1 Cell culture capacity 5K x 6 = 30,000L
- Plant 1 Capability Liquid & Lyo vials
- Plant 1 CGMP ready Jun. 2013
- Plant 1 Laboratories QC Laboratory
- Plant 2 Cell culture capacity (1.5K x 10) + (1K x 2 SUS) + (1K x 2 SS) = 154,000L
- Plant 2 Capability Liquid & Lyo vials
- Plant 2 CGMP ready Fed. 2013
- Plant 2 Laboratories PD Laboratories
- Plant 3 Cell culture capacity 15K x 12 = 180,000L
- Plant 3 Capabillity Fed-batch with N-1 perfusion capability
- Plant 3 CGMP ready Oct. 2018
- Plant 3 Laboratories QC Laboratory, PD Laboratories
- Plant 4 Cell culture capacity (15K x 12) + (10K + 6) + (2K + 8) = 256,000L
- Plant 4 Capabillity Multi-scale, digitalizations, automation, eco-friendly
- Plant 4 CGMP ready Expercted by. 2023
- Plant 4 Laboratories QC Laboratory, PD Laboratories
Samsung Biologics offers ‘one-stop services’ that not only includes contract manufacturing but development and testing services too, allowing us to support the full product lifecycle for our customers. We are fully equipped to accommodate projects of all shapes and sizes while reducing manufacturing time and overall cost.
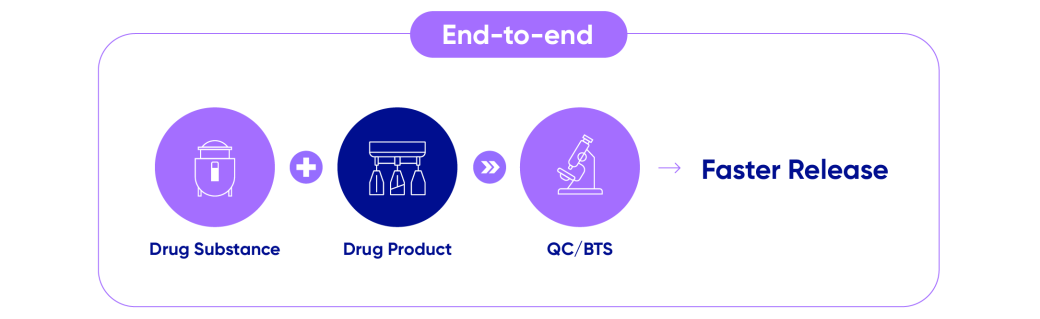
- Drug Substance
- Drug Product
- QC/BTS
- Faster Release
By offering fully-integrated services to our clients, we can ultimately reduce the potential for time delays as well as the risk of information leaks whilst ensuring consistent quality. For example, Samsung Biologics’ drug product (DP) services recently reduced time for tech transfer to 2-3 months - half the industry average of 6 months - for verification of batch production to expedite the process and deliver urgent biopharmaceuticals to treat COVID-19.
As a means to further increase client satisfaction, we also have state-of-the-art manufacturing capabilities, such as N-1 Perfusion* and EQUIS**, to improve cell density, reduce production time, and improve productivity, as well as advanced digital technologies such as our ‘Live Virtual Tour (LVT)’ system which was preemptively introduced in early 2020 in light of COVID-19. The LVT gives our clients and regulatory agencies remote access to our online system anywhere in the world and the ability to conduct virtual due diligence safely and effectively.
*N-1 Perfusion: Advanced cell culture technology that improves productivity by reducing production time.
**EQUIS (Enterprise Quality Unified Information System): A system that can record and manage documents and quality records in real time.
The Final Hurdle: Successful Aseptic Fill & Finish
Samsung Biologics has shown a rapid growth rate for its aseptic fill/finish business area since it started the business and has become well-known for its quality and speed. Aseptic fill/finish is the final stage of the manufacturing process before patient administration, and as such requires adherence with complex standards for facility operation and management, as well as manufacturing processes to ensure thorough aseptic treatment while maintaining the strictest care for quality.
In addition, the stability for product quality is crucial for this particular stage as it is the only process where the product is externally exposed prior to administration. Samsung Biologics has obtained a total of 16 approvals for its aseptic fill/finish from major agencies including the U.S. Food and Drug Administration (FDA), the European Medicines Agency (EMA), and the Japanese Organization for Medical Devices (PMDA) giving us an impressive track record when it comes to successfully completing aseptic fill/finish projects.
We also have plans to expand our facilities for the manufacturing of both mRNA vaccine drug substance and drug product allowing us to commence manufacturing for vaccines in 2022 and become Asia’s central hub for vaccine supply.
Fully Integrated CDMO Partner: A Track Record to Inspire Trust
To date, we have multiple manufacturing contracts with some of the world’s leading biotech companies, including the manufacturing of COVID-19 treatments and vaccines. Samsung Biologics has obtained a total of 92 global approvals from international certification agencies as of May 2021 and is still growing, affirming its leading capabilities and bolstering its position as a recognized and trusted CDMO partner.
Since its establishment in 2011, Samsung Biologics has continued to evolve to ensure we continue to manufacture high-quality biopharmaceuticals for our customers. We do this through our dedication to continuous innovation and by ensuring the strictest care for quality.
Samsung Biologics was awarded the ‘CMO Leadership Awards,’ an industry-recognized award, in 2013 for successfully achieving client satisfaction and quality competitiveness, while quickly responding to changes in the market environment and providing life-saving solutions to patients worldwide.
Our team continues to offer a fully integrated, end-to-end manufacturing services to its clients to enhance both the global and local supply network of biopharmaceuticals and to save lives of many people in urgent need worldwide.
- CDO
- CGMP
- ADC
- Bio Campus
- IR
- CMO
Share article